Concrete

Concrete designed for a good foundation.
- The Romans made concrete by combining lime plasters with volcanic soils from Pozzuoli, forever after to be known as pozzolans. Many of their magnificent structures still exist 2,000 years later because they made concrete very well (unlike most modern concrete) and they did so with no fossil fuels.
- We mimic that quality here by reusing industrial waste products from electrical generation and steel production to replace Portland cement. Portland cement—the glue that holds sand and gravel in the form of concrete—is made by baking limestone, and its production accounts for 8% of the carbon dioxide emissions of humanity. So replacing some or most of it in concrete mixes yields better concrete and greatly reduces its carbon footprint.
- After grading the building pad, we also discovered that it is much cheaper—and has much less ecological impact—to work with the soils onsite rather than exporting or importing truckloads of earth, as is commonly done. The house bears on drilled piers that penetrate the fill areas and secure the house to bedrock; “sitting lightly on the land.”
Concrete details
Display More [+]How green is our concrete? The short story –
- About 262,000 pounds less carbon went into the air for having pursued a green agenda with the concrete, a 37% carbon reduction that was dollar-cost neutral. Our concrete mixes ranged from 50 to 70 percent slag. The end result 375 pounds of carbon per cubic yard of concrete vs. more typical values ranging from 400 to 520 pounds per cubic yard.
- Regarding the replacement of Portland Cement, we used ground, granulated blast furnace slag, aka "slag", to displace Portland cement at 170 Mapache. We installed:
- 643 yards of 50% slag replace mix - replacing 1768.25 sacks of Portland cement.
- 81 yards of 70% slag replace mix - replacing 311.85 sacks of Portland cement.
- In other words, a total of 2,080 sacks of Portland cement were NOT used compared to "ordinary everyday" concrete, which equals (at 94 lbs per sack) 195,520 pounds of cement, which represents 195,520 pounds of carbon not emitted – just from minimizing the cement.
- Achieving that required only a clear and consistent mandate from the clients, and a modest amount of extra communication between the engineer, general contractor, and suppliers. The resulting concrete is of higher quality by every significant metric than would be its conventional counterpart — there was no downside to “going green”. Still, though there is no reason not to use green concrete, the practice has yet to become widespread in an industry extremely resistant to change. The technology is there, clients have to push for it.
The longer story
- First, some caveats: Our numbers in this short report are accurate but not very precise, because carbon accounting is still new. Data are spotty, imperfect, and localized (a study done in London will show different results from the same type of research in Reno or Shanghai). Further, there is the problem of boundaries: where do you begin and end accounting? Our overall figure of 375 pounds of carbon per cubic yard of reinforced concrete passes the test of reasonability in the context of other studies.
- Material efficiency and energy efficiency are very different. With building materials, we cannot get and usually don’t want appreciable reductions in weight or mass; what we want is more utility for less energy/carbon cost. With concrete, that boils down to glue — the stuff you mix in with water, sand and gravel to create artificial rock, aka concrete. Modern practice relies entirely on Portland cement as glue, which is made by baking and grinding limestone. The combination of baking (with fossil fuels) and calcining (driving carbon from the limestone) is why the cement industry is responsible for 8% of carbon dioxide emissions worldwide. Most of the trick with green concrete, then, is to replace as much of the cement as practicable with common industrial by-products that happen to be very well suited for the purpose. We replaced a range of 50% to 70% of the Portland Cement in the various applications across the project. In every other respect, such as size of grade beams, thickness of slabs, and amount of reinforcing steel, the project is consistent with conventional practice.
- Actually, the foundation and structure are slightly beefier than “normal”, in keeping with the twin mandates for extra high seismic safety (makes no sense to build a green building that could potentially fall down within 30 years during an inevitable earthquake) and very long service life. The extra durability of 200 years+ vs. normal 50 years adds to the “greenness” of the project by eliminating material demands on future generations. Ostensibly, this makes for a fourfold increase in material efficiency. But, again, the numbers are quite fuzzy, and this extra durability is not accounted for here in this report’s conclusions.
Carbon emissions from concrete work in Portola Valley, CA in pounds of carbon (or carbon-equivalents)
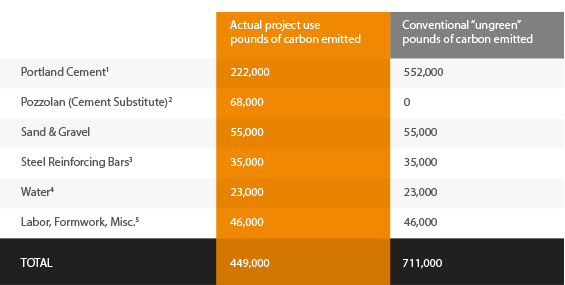
- Portland cement taken to emit one pound carbon per pound of cement (multiple sources)
- Pozzolans (slag and ash) taken to emit 0.2 pounds carbon per pound of pozzolan “slag” is ground, granulated blast furnace slag, a by-product of steel production “ash” is fly ash, a by-product of coal-fired power (the dust collected from the smokestack). (Some would say this number should be zero; 0.2 is used to account for transport & some of carbon cost of source process; an arguable but precedented figure.)
- Steel taken to emit 0.42 pounds carbon per pound (Univ. of Bath database)
- Based on Calif. Energy Commission numbers – 0.1 lbs. carbon per lb. water.
- Labor carbon is overwhelmingly due to the fuel used by workers moving to & from site
Proportional carbon emissions from concrete work

- The Project